The ability to simulate seats is a powerful tool in your modeling repertoire. However, even more powerful is the ability to simulate a person's comfort in your newly designed seat. One of the biggest hurdles to simulating comfort is that it is inherently subjective while manufacturers require an objective method to truly quantify the thermal performance their seats.
How do we solve this? How do we find objective data for what is a subjective response?
By using the simulation technology of a human comfort model and validating those measurements using manikins.
In our last blog about seat simulation, we covered virtual seat characterization and validating the thermal properties and seat behavior using a STAN manikin. Today we continue with the same advanced simulation methodology but we'll take it a step further by understanding how comfortable a human would be in the cabin environment and what role the seat plays in that exchange.
Take All Thermal Factors into Account
It is important to use a human comfort model that will take into account the seat thermal performance since there can be significant heat transfer at the contact surface whether you're simulating a passive or active seat. Simple environment-based comfort metrics (PMV, EHT) will not account for such heat transfer. It is important to use a physiology-based comfort metric which will be impacted by all the models of heat transfer. You can then simulate all thermal effects in order to have a holistic view of the level of comfort the occupant would feel.
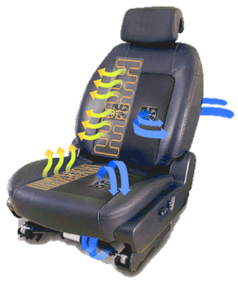
Both the seat's passive and active properties play a role in understanding the thermal comfort of a seat. First off, the seat characterization process will provide you with the effective thermal resistance, capacitance, and vapor permeation of the seat. If you are simulating an active seat, you can then characterize the active properties such as heating and cooling power, ventilation effect, and response time. You can then apply these effects to simulate how the active characteristics of the seat impact the comfort of the human occupant in the context of a vehicle cabin. This type of seat simulation allows you to objectively compare how one seat would perform versus a different seat design, provided you characterized both seats. It also allows you to see how a given seat would influence comfort in different environments or scenarios.
Validate Your Comfort Results – Objectively!
Once you have modeled your complete seat design and simulated it with a human comfort model, you can validate your results using an active manikin. Active manikins can provide the objective data you are seeking that will help you to make substantiated design revisions to your seat for how it reacts in the cabin of your vehicle design. These manikins are considered human surrogates. Using a matrix of sensors that cover the manikin, they measure the comfort of the existing environment by considering air velocity, air temperature, radiant heat flux, and relative humidity. The Newton manikin, in particular, reacts just as a human would; they shiver when they're cold and sweat when they're hot. They can evaluate the environment the same way a human would, yet are completely objective – allowing for unbiased, reproducible tests.
Design Efficiently with Total Cabin Simulation
Once your seat is characterized, simulated, and then validated using an active
manikin, it is important to integrate your seat design into your complete cabin model. Total cabin comfort can be simulated by modeling HVAC, environmental effects, seats, as well as human impact. This type of full cabin comfort prediction will give you a holistic view of all factors affecting the occupant's comfort. This allows for better design choices, creating efficiency between the different parts of the system as well as between the teams working to design the car.
Moving from simulation to validation with manikins to complete cabin modeling allows you to create prototypes with fewer design flaws. This type of "front-loaded" design methodology is vital if you are looking to develop an innovative process and push the boundaries on your designs. This process not only reduces the expense of prototypes but time, energy, and frustration which are inevitable in the test-and-fix methodology.
Apply an Objective Methodology for Comfort
ThermoAnalytics has developed an objective methodology to quantify the thermal performance of seats in terms of thermal comfort. For our advanced simulation methods, we used TAITherm and our Human Thermal Extension along with Thermetric's Newton manikin (pictured to the right). These tools couple seamlessly, allowing us to simulate and validate all human physiological responses and the interactions with the cabin environment. We offer both services and software for optimizing seats using these advanced simulation technologies.
The seat modeling methods we have proposed so far discuss measuring seat characteristics with the STAN manikin and validating the comfort of those seats in a cabin environment using an advanced human comfort model. In our next blog on seats, we will discuss ThermoAnalytics’ simulation method that involves explicitly modeling the materials, shapes, and interactions of all the seat components based on your CAD data. Then validating your geometry-based model with STAN measurements once a physical seat of that design has been built. This more explicit modeling process allows you to examine the seat design in more detail and simulate changes to individual materials, thicknesses, and stack-ups.
If you want to know more about how a simulation methodology like this could improve your design process, please don't hesitate to reach out to us.