Packaging constrictions in new vehicles dominate the positioning and organization of components within the engine compartment. With less space and more temperature sensitive components, (plastics for lightweighting, infotainment, and electrical components) thermal management becomes an increasingly critical aspect of vehicle design. Component hot spots can lead to safety, durability, and warranty issues. Careful consideration of component placement and heat shields is mandatory to avoid costly late-stage fixes.
Traditional Testing Does Not Allow for Adequate Optimization
Traditionally, thermal protection teams use wind tunnels and road tests to determine a management strategy. With simulation, vehicles can be optimized for performance, sensitive components, and passenger comfort. Simulation can accurately predict the complex interactions between conduction, convection, and radiation, especially for very hot parts. Although testing on the road and in wind tunnels will be necessary to verify simulation predictions, the use of software allows you to focus on the most critical areas and bring them as close to the final design as possible.
Vehicle thermal management is typically based on two or three steady-state load cases and a thermal soak. Thermal soak occurs when a vehicle is driven at high speeds or under a heavy load and then shut off to begin a cooling down period. After stopping, airflow is limited, and components near the exhaust system become very hot. These temporary high temperatures could cause significant issues depending on the layout of your vehicle design.
Coupled, Transient Simulation Will Provide the Answers You Need
The two major challenges to accurately simulating this activity are the transient behavior and coupling temperature and fluid results. Although a CFD code is capable of solving the transient thermal-fluid problem, the computational requirements are burdensome, even with today's high-performance parallel computer systems. A coupled simulation is a better solution.
A coupled simulation that uses a fast, transient thermal solver and a CFD code is quick and accurate. You can make variations and rerun the simulation to find your answer much faster than with testing or running only a CFD code. A fast, transient solver allows you to test many design variations in the same amount of time it would take to test only your assumed best two or three designs.
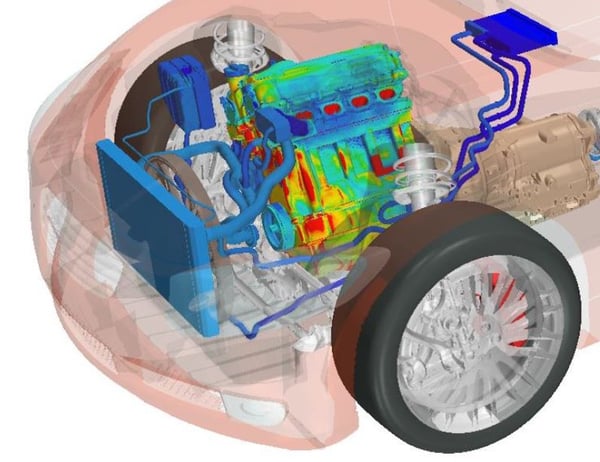
Simulation Methods Provide More Answers to More Scenarios
Under a typical production schedule, there is only time to test a couple of worst-case scenarios to determine the highest temperatures the components will reach. The thermal risk is then determined by those extreme temperatures instead of the amount of time those components will be exposed to high temperatures. Radiative and convective heat transfer in the underhood/underbody environment may cause parts to exceed design temperatures limits
Transient Drive Cycle Simulations are the Next Step
Driving cycles also affect how sufficient the component layout will be. With a fast, transient simulation tool you can test multiple driving scenarios for your vehicle design, not just the most common ones. The same amount of time it would take to model your two or three "best" designs, you could move forward with an optimal design by simulating many types of scenarios, from extreme to daily driving occurrences. Many of these driving conditions, such as city driving or extended soaks, require transient modeling as components may not quickly reach steady-state.
Transient Drive Cycles are Important For Battery Lifetime Predictions
Another reason to simulate more than extreme drive cycle cases would be to predict battery lifetime. As hybrid electric and electric vehicles become more ubiquitous in the automotive market, battery lifetime performance is becoming an issue of greater importance. You will ensure that the battery will operate at a safe temperature, but even though the battery can perform at that temperature, doesn’t mean it will continue to function optimally at that temperature. With a growing battery market, lifetime operating capacity will become a differentiator. Ensuring that your battery has a similar capacity for seven years instead of 5 years may set you apart in the market. Batteries are another strong motivation for simulating daily drive cycles instead of only the most extreme conditions.
Advancing Simulation Methods Will Save You Valuable Time
Simulation methodologies are becoming more advanced which allow us to get closer to the ideal designs we are seeking to provide. The results you derive from the model can be validated against your test data but starting with simulation allows you to rule out many design options before building your prototype. Getting closer to the ideal design earlier in the production process will save you valuable time later on.
We hope this discussion gave you some food for thought. If you have any follow-up questions about our methodology, which utilizes a fast-transient thermal solver, contact us, tell us a bit about your thermal problem, and we would be glad to help you find a solution that will work for you.