As the automotive industry continues to increasingly emphasize user-centered design philosophies, the wants, needs, and comfort of the actual humans inside the vehicle are afforded greater and greater attention. Of course, migration to user-centered design methodologies do not happen overnight, but by and large the trend lines are encouraging.
But the parallel growth in the electric vehicle and hybrid markets injects a bit more urgency into its adoption for certain OEMs. In such vehicles, of course, energy efficiency is paramount; at the same time, such powertrains do not benefit from readily available waste heat as do their conventional counterparts.
As a result, the perfect solution is one that not only solves for human comfort, but one that does so while optimizing for energy efficiency as well.
Can Comfort Be Simulated?
In EV and hybrid vehicles, cooling or heating a cabin is going to require some amount of energy. Obviously, the more energy the vehicle consumes achieving a certain desired cabin temperature, the less it can devote to other critical tasks. But advanced design teams are less concerned with hitting a specific temperature target, but rather finding and achieving the precise conditions under which the human in that cabin feels comfortable.
When the change in objective becomes human comfort and not, say, 74 degrees Fahrenheit, the potential for energy conservation becomes potentially game changing. In other words, how much energy could you save if you didn’t need to cool an entire cabin, but only the human in the driver’s seat?
It is these types of calculations that OEMs are increasingly insistent on discovering and leveraging for both efficiency optimization, as well as design and engineering optimization, as design modifications can be front loaded in the product lifecycle and at considerably lower cost. In fact, it is quite possible (and often the case) that simple design modifications can have a significant impact on human comfort. Perhaps the seats need to be cooled and vented. Perhaps the HVAC should locally cool the driver’s face or torso. The possibilities might be endless, but easily discoverable, if the designer has the proper targets in sight and access to the latest technology.
Naturally, this needn’t and shouldn’t be guesswork. The ultimate challenge is getting an objective evaluation of human comfort, when human comfort is inherently subjective. However, prototyping and human testing incurs costs of both time and money -- resources that OEMs might better invest elsewhere.
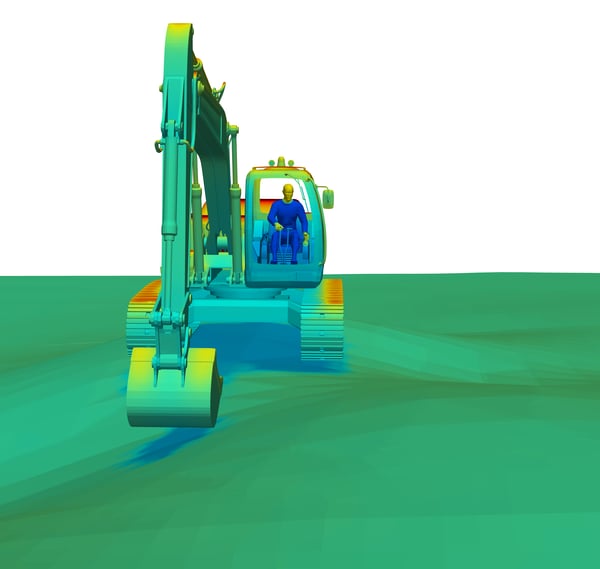
Thanks to advancements in simulation technology, coupled with a better understanding of human comfort (see: Berkeley Comfort Model), designers and engineers have access to an extremely reliable and predictive methodology to accurately model and design for human comfort. The most advanced among them are harnessing the power of high-fidelity 3D comfort simulation to predict air and surface temperatures, as well as actual perceived comfort of the human occupant.
The Best of Both Worlds: Simulated and Real
The best-case scenario is to couple the high-fidelity 3D thermal software with CFD, used to predict airflow patterns inherent in the vehicle’s HVAC system design. Better yet, designers can even easily couple this paired solution with 1D analysis tools, such as GT-SUITE, and a tool that includes an advanced physiological model, such as the Human Thermal Module, to get an even more robust model of the complete HVAC system and how it interacts with human comfort.
Keep in mind, we are trying to design for human comfort, not cabin temperature. So, by that very definition, a designer needs to understand that human’s comfort in the real world...under transient conditions. A CFD solution alone will not be able to efficiently run the transient analysis. Coupling allows the design team to vary drive cycles and simulated heat loads to examine how the vehicle design performs in dynamic cool-down situations, or in city driving mode versus highway driving, or at high external heat loads and extremely cold climates (to name only a few scenarios).
The bottom line is that simulation allows you to raise infinitely more hypotheticals to identify how a cabin occupant perceives his or her comfort, in a way that is very conscious of the bottom line. Simulation cuts weeks or months out of a product lifecycle, along with considerable investments in financial resources.
Many teams are even going so far as to compare real-world tests against the simulations to validate the modeling data against an occupant’s reported perceptions of comfort in the ultimate production vehicles or physical prototypes...and the results reveal remarkable accuracy.
Learn More
The critical task facing all OEMs -- but EV and hybrid manufacturers especially -- is to implement a simulation process that can be applied to any future design program, which would further save both time and money down the road. But only if you can simulate and predict actual human comfort can you reliably design an HVAC system that meets your target objective of optimizing efficiency and achieving passenger comfort. In other words, if you solve for human comfort once, you can apply that understanding to evaluate similar designs more rapidly.
.jpg?width=600&name=alejandro-salinas-189861%20(2).jpg)
When done correctly, not only do you maximize human comfort -- a prevailing goal industry-wide -- you do so while optimizing energy efficiency. That combination of achieved objectives has more and more OEMs taking notice...and taking meaningful steps to get there.
We go into greater detail about human comfort simulation and our Human Thermal Module here, and would welcome the opportunity to demo the solution for you whenever you’re interested. If you have any specific questions about human comfort simulation, please do not hesitate to contact us for more information.