The comfort experienced by a customer in your vehicle is increasing in importance. Not only is cabin comfort used as a market differentiator for new vehicles, but as new technology like autonomous cars appears on the horizon – a person's awareness of their comfort will increase. Seats, specifically active seats, are a significant contributor to a person's comfort.
Creating an efficient method for modeling seats is important to keep up with developing technologies. Understanding how your seat should be designed can also help seat designers deliver informed decisions to suppliers. Suppliers will also be able to demonstrate how their components will be beneficial to the seat design, creating a better dialogue between designers and suppliers.
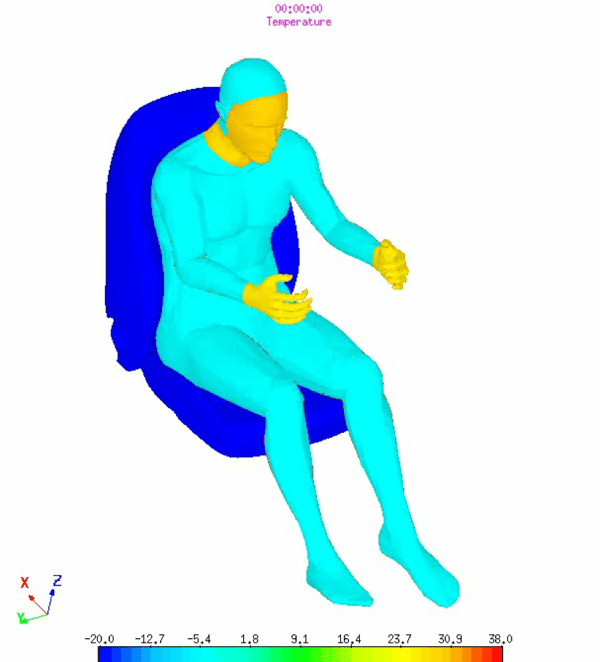
Advanced simulation methods present a new way to design seats – creating your design virtually. Start with a fully detailed CAD model of your seat, modeling all of the seat components such as the cushion, frame, layers of padding, and any active heating or cooling components. This type of explicit model will allow you to simulate all of the physics of the heat transfer in your seat.
With this type of simulation, you can make design changes and see how they affect the thermal properties of your seat. For example, you can model a change in a material or cushion and see how it affects the thermal conductivity. You can also look at the location and density of your heating wire or mat to see how changes affect heat transfer to the occupant. You can also look at other factors such as mass reduction and energy efficiency.
To truly understand the thermal properties of your seat components, you will want to simulate the materials compressed as if a person were sitting on the seat. It is important to understand how the thermal properties of your seat will change once they are compressed under the weight of a person. When a cushion is compressed, air is forced out of it and it conductivity increases. Including the compressed shape in a simulation software requires "morphing" a technique used to simulate the compression of the seat by bending and twisting the CAD geometry. For the thermal model, you will also need to know the thermal property measurements of your materials in compressed and uncompressed states. Then you will be able to model a seat when it is occupied (compressed) and when it is empty (uncompressed) as it would be during a solar soak.
If coupled with a human thermal and physiology model, you will also be able to model the sensation (physiological) and comfort (psychological) of your occupant based on your design. This type of human simulation will give you an objective way to test your design vs. the more subjective method of testing – using real humans and expensive prototype seats.
One key aspect of understanding human thermal comfort is understanding the person's environment. Not only the car that they are getting into but the environment that they have come from. Creating realistic starting scenarios will help you understand just how comfortable the cabin of a car would be for someone. If it is a cold, winter day and they are wearing jeans, how long does it take for them to feel comfortable using a heated seat? Preconditioning both the vehicle and the individual will give you the most realistic starting scenario. Simulation allows you to easily run multiple preconditioning scenarios and assess their impact on time to comfort.
One of the biggest benefits of using this type of simulation method is that you will be able to design your seat virtually before any prototypes are available. You can perform design analysis on the seat, modeling the different materials since it is explicitly built-up. With the ability to perform design analysis on a virtual model and replicating what a real seat would do, you will be able to save yourself time, frustration, and money during the prototyping phase of your design.
While building up a detailed model of a seat and capturing these important details takes a good amount of work, the payoff later down the road can be worth it. There are some choices to be made regarding optimizing your effort vs. how much accuracy is necessary to get the answers you are looking for. However, with advancing simulation tools, this question becomes a little easier to answer as new tools allow more detail while still retaining acceptable run times.
One such tool is our thermal simulation software TAITherm, which allows you to model an accurate solution to make confident design decisions but also offering a run times of minutes to hours. When coupled with our Human Thermal Extension, the design process described above is not the future of simulation but a reality for today's seat designers and suppliers.
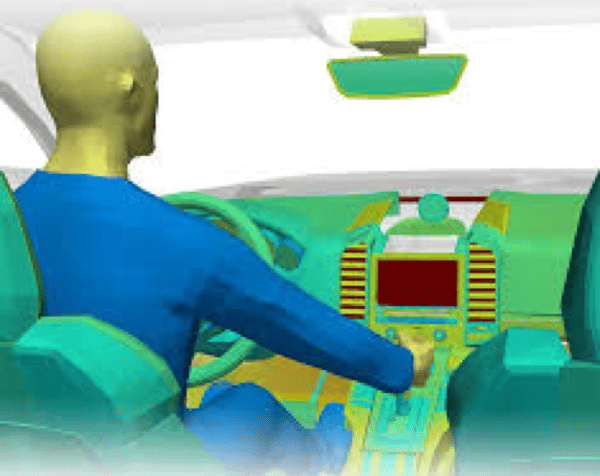
TAITherm and the Human Thermal Extension will allow you to simulate your seat with all components, understanding the thermal sensation and comfort of your seat within the context of the entire cabin. The Human Thermal Extension delivers one of the most sophisticated thermo-physiological models, allowing you simulate what a human would feel and mitigate the challenges of testing seats with real humans. TAITherm offers a way to combine the techniques described in an efficient and realistic virtual design process.
Curious how this type of simulation method could improve your design process? Let’s set up a demo and we can show you exactly how TAITherm and the Human Thermal Extension can simplify your workflow.