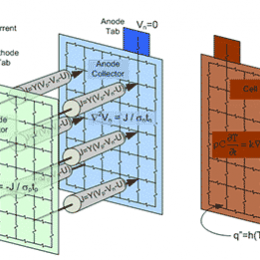
The growing interest in, and early adoption of, hybrid and electric vehicles has created a surging demand for lithium-ion batteries in the automotive, military, and other industry sectors.
But as is the case with so many emerging technologies, the early years can be fraught with the risk, time delays, and unforeseen expenses inherent in experimentation and best-practice pursuit.
As more and more people show a willingness to adopt (or even demand) advanced battery technologies to support their eco-friendly sensibilities — the reliability, safety, and predictability of lithium-ion technology becomes increasingly critical for manufacturers and suppliers looking to capture this market and its demand
New Technology Emerges to Support Emerging Technology
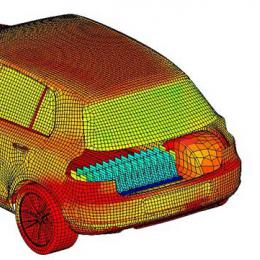
Publicized reports of battery failures, less-than-optimal performance, and even safety hazards in some cases remind us there's a learning curve. To those making and selling the products in which this new battery technology is being used, learning curves mean expense. And delays. And, worse, liability.
Testing is needed. Modeling is illustrative. Improvements come with time. And all of that comes at an expense in real terms and opportunity cost.
Fortunately, advanced technologies are helping OEMs, and suppliers do this testing, experimentation, and validation virtually, eliminating much of the time, expense, and risk in the process.
Take, for example, the thermal management of lithium-ion battery systems — perhaps one of the most critical aspects and predictors of lithium-ion battery performance. Temperature not only greatly influences the battery's performance and storage capacity, but it also has a direct safety correlation for which it is paramount to control.
Real-World Modeling, Real-World Savings
One way to test, measure, and predict the performance and safety of advanced lithium-ion battery systems is to expose them to the conditions that such batteries might encounter in the real world. But even traditional methodology, typically based on steady-state analysis, captures mere snapshots in time (e.g., How does the battery respond to steady worst-case environmental/operating conditions?).
By way of contrast, transient analysis (or that which simulates real-world time-varying fluctuations in the conditions to which a battery may be exposed), goes far beyond unrealistic “snapshots.” For example: How does a battery perform during changing environmental conditions when the vehicle suddenly must go uphill, or if it is pulling a load, or at various stages in the battery charge lifecycle? What about after the vehicle has been running for a long time? Such analytics are true measurements of real-world predictability and can mean the difference between mere testing and actual validation.
In collaboration with the National Renewable Energy Laboratory (NREL), a coupled thermal-electric model for battery cells and packs has been developed and implemented into the existing thermal modeling software, TAITherm. This technology allows OEMs and suppliers to save considerable time, money, risk, and testing by allowing for “virtual prototyping.”
With the ability to put a battery system in all kinds of environments, as well as all kinds of usage scenarios, and measure how they respond and perform over time, manufacturers can reliably move forward with new technology with greater confidence by knowing how well it works before it is even taken to market.
With what is referred to as “high-fidelity modeling,” it does not have to make as many assumptions and approximations because the system can simulate reality far more accurately than steady-state analysis or limited testing ever could. Steady-state analysis may very well account for worst-case scenarios, but it also can result in a “factor of safety” that is costly and unnecessary because it does not represent reality. By its very nature, the transient analysis will account for real-world worst-case scenarios and thus is much more accurate than any results from steady-state assumptions.
A published and thoroughly researched white paper describes a thermal and electrical analysis to concurrently evaluate all environmental and drive cycle scenarios against a battery's charge and discharge capacity. The results clearly demonstrate the reliability and importance of simulating actual, real-world conditions that lithium-ion batteries' thermal management systems could encompass.
The Future is Now
As hybrids and electrics continue to gain market share and as the military continues to expand the boundaries of experimentation in this space, greater demand and heightened reliability expectations will be placed on advanced battery systems. What not too long ago seemed like an aspirational future is quickly becoming a real-world actuality.
Battery systems must keep pace with demand and their rigorous requirements, and manufacturers implementing them will be on the front lines of this evolution. As the learning curve necessarily flattens, what better way to prepare for real-world eventualities than simulating real-world performance testing?
For more information about ThermoAnalytics’ Battery Extension for the proprietary TAITherm system, visit our website.
If you want to learn more about using TAITherm to maximize your EV range in cold-weather environments, please feel free to request a live demo of our software.
Visit our website at suppport.thermoanalytics.com for
- FAQs
- Webinars
- Tutorials
Get help from our technical support team: