As an automotive designer, cabin comfort is the foundation of customer satisfaction and ultimately, product sales. The rising tide of battery-powered electric vehicles brought a new design challenge to automakers, pushing them to find a way to optimize the sub-systems in the vehicle while avoiding enormous draws on battery power at the same time. This problem is addressed by running transient human thermal and battery tests to optimize for HVAC and battery systems. In this blog, we will understand how an automated coupling process can provide an optimized solution while avoiding the long solve times of highly transient problems.
Optimizing Transients Requires Coupling
Running individual transient human thermal and battery simulations is an extensive process due to the amount of information needed to deploy each test, and the level of accuracy these simulations demand to provide useful results. Among long solve times, the user must run an analysis on the simulation results and evaluate the outcomes to determine the best path forward.
In the fast-paced automotive world, this method isn’t performing quickly enough for designers who are in dire need of optimizing battery range and cabin comfort on electric vehicles. Electric vehicles are gaining in popularity but the 50%-60% loss of battery range that their HVAC systems cause is a major problem for OEMs and EV customers. Consumer anxiety over limited battery range is a problem the automaker must overcome to obtain growth and a competitive edge in the market. To solve for optimized battery range, they can use CFD and thermal simulations to evaluate the cabin airflow and environmental effects on the battery and quickly offer a solution to maximize thermal comfort with minimum energy consumption.
Coupled Simulation Reforms the Design Process
Rather than running fluid and thermal analyses in a single software package to look at the airflow, cabin comfort, and temperature limits on the batteries, coupled automation software programs will pair segregated solvers and analyze an assortment of design variations. With this information, it will then suggest the best method to reach optimal human thermal comfort and/or battery range at the same time. To get started, the software requires the user to contribute necessary solving inputs including thermal and CFD models of the cabin, the characteristics of the HVAC system being modeled, and the desired end goal of the simulation.
Using this data, the automated coupling software will run multiple transient simulations, analyzing exterior heat transfer from the vehicle and the flow inside the cabin. For cabin warm-up, cabin cool-down, or battery discharge, a common coupling method is Pseudo-transient coupling, which enables testing the maximum number of design iterations in a short amount of time by linking multiple snap-shots from the CFD code with a thermal analysis from start to finish. This process provides solutions at a much quicker rate while still displaying a fully-transient solution.
What is CoTherm Capable of?
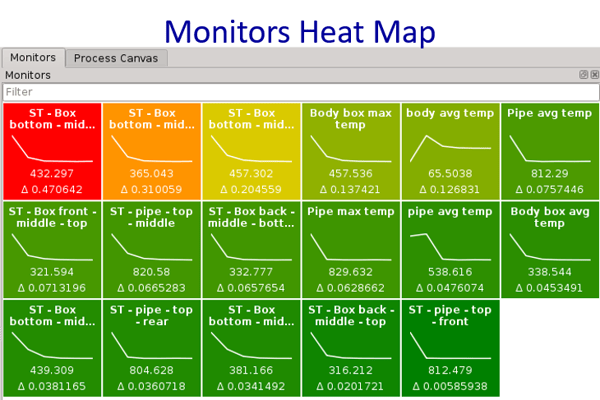
ThermoAnalytics’ has its own coupled simulation software. Built by our team of highly-skilled software engineers, CoTherm is designed to solve all levels of coupled simulation problems. In less than one day of solving time, the software can offer transient flow and temperature predictions of the cabin or battery enclosure. Using this prediction, teams can choose an accurate HVAC system & battery capacity depending on sizing and comfort predictions they received from the simulation. By keeping track of resources, tasks, and notes in its intuitive interface, the user can try more design iterations and view real-time results in a color-coded heat map to find the most optimal solution in the least amount of time.